Electrical Equipment Safety in Workplaces
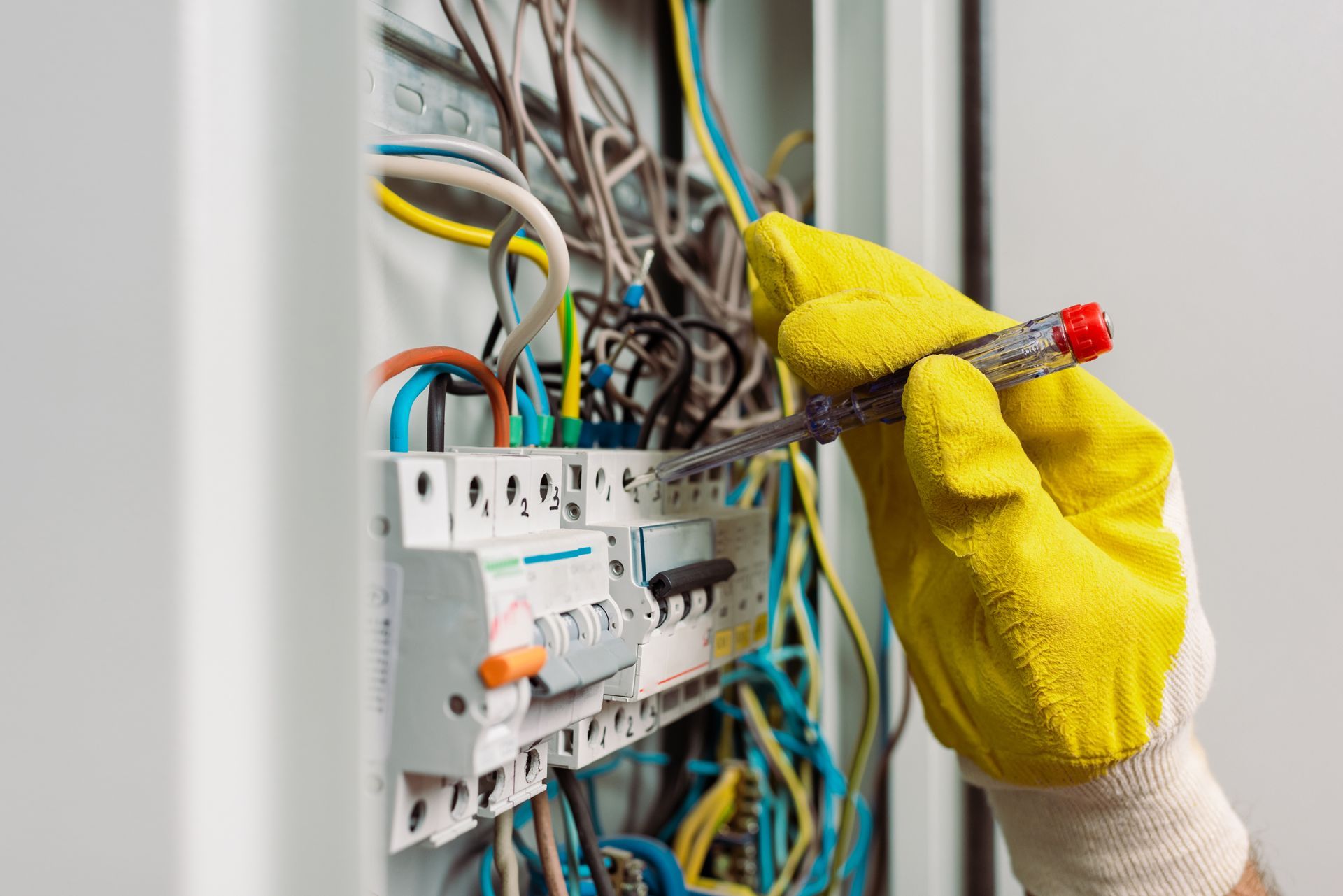
Ensuring electrical equipment safety in the workplace is crucial for protecting employees from electrical hazards and maintaining a safe working environment. Electrical accidents can result in severe injuries, fatalities, and significant property damage. Below are key considerations and best practices for maintaining electrical equipment safety in workplaces.
1. Regular Inspections and Maintenance
Conducting routine inspections and maintenance of electrical equipment is vital to ensure that all components are functioning properly and safely.
- Checklist for Inspections:
- Look for frayed or damaged cords and plugs.
- Check for signs of overheating or burning.
- Ensure all safety features are operational.
- Confirm that equipment is properly grounded.
- Schedule Regular Maintenance:
- Establish a maintenance schedule for all electrical equipment.
- Engage qualified personnel to perform inspections and repairs.
2. Proper Use of Equipment
Educating employees about the correct use of electrical equipment can significantly reduce the risk of accidents.
- Training Programs:
- Implement training sessions on the proper use of equipment.
- Cover topics like safe operating procedures, emergency shutdown procedures, and recognizing hazards.
- User Manuals:
- Provide access to user manuals and safety guidelines for all electrical devices.
3. Use of Personal Protective Equipment (PPE)
Providing the appropriate PPE is essential for employees who work with or near electrical equipment.
- Required PPE Includes:
- Insulated gloves to protect against electric shock.
- Safety glasses to shield eyes from sparks and debris.
- Electrical hazard-rated footwear to prevent shocks.
4. Ensuring Adequate Training and Knowledge
Employees must understand electrical safety protocols and emergency procedures to act quickly in case of an incident.
- Comprehensive Safety Training:
- Offer training on electrical safety standards and regulations.
- Conduct drills for emergencies such as electrical fires or shocks.
5. Clear Labeling and Signage
Clearly labeling electrical equipment and using signage can help prevent misuse and inform employees of potential hazards.
- Labeling Guidelines:
- Label circuit breakers and panels to indicate their function.
- Use hazard signs to warn employees of electrical risks in specific areas.
6. Avoiding Overloading Circuits
Overloading circuits can lead to overheating and fires. Proper management of electrical loads is essential.
- Load Management:
- Distribute electrical loads evenly across circuits.
- Avoid using multiple high-wattage devices on the same circuit.
7. Safe Work Practices
Implementing safe work practices can mitigate the risks associated with electrical equipment.
- Key Practices Include:
- Always unplug equipment before servicing.
- Keep work areas clean and free of clutter to prevent tripping hazards.
- Use extension cords rated for the intended load and avoid daisy-chaining multiple cords.
8. Emergency Preparedness
Being prepared for electrical emergencies can save lives and minimize damage.
- Emergency Protocols:
- Create and communicate a clear emergency response plan.
- Ensure that employees know how to report electrical hazards and accidents.
- Provide access to fire extinguishers rated for electrical fires.
9. Investing in Quality Equipment
Using high-quality electrical equipment can reduce the risk of malfunctions and accidents.
- Selecting Equipment:
- Purchase equipment that meets relevant safety standards and certifications.
- Opt for equipment designed for the specific conditions and demands of the workplace.
10. Consulting Professionals
Engaging qualified electricians for installations, repairs, and inspections ensures compliance with safety regulations.
- Professional Services:
- Hire licensed electricians for installation and maintenance of electrical systems.
- Schedule periodic audits of electrical systems to ensure safety and compliance.
Conclusion
Electrical equipment safety in the workplace is a shared responsibility that requires commitment from both employers and employees. By implementing proper safety protocols, providing adequate training, and maintaining equipment, businesses can significantly reduce the risk of electrical accidents and create a safer working environment. Prioritizing electrical safety not only protects employees but also enhances productivity and reduces potential liabilities for the organization.